Stock Code: 300855
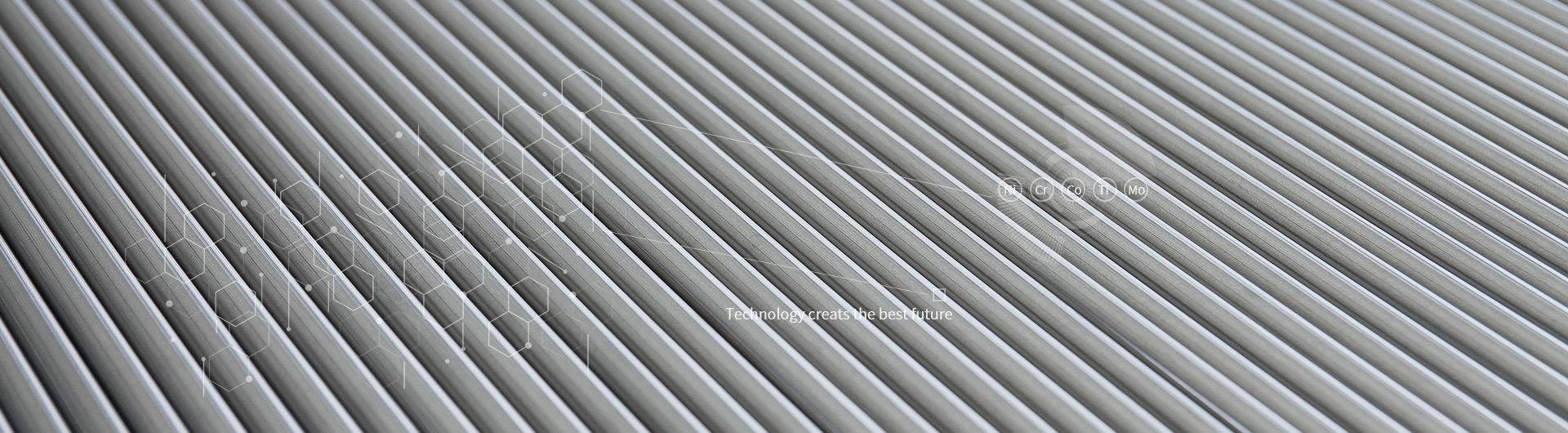
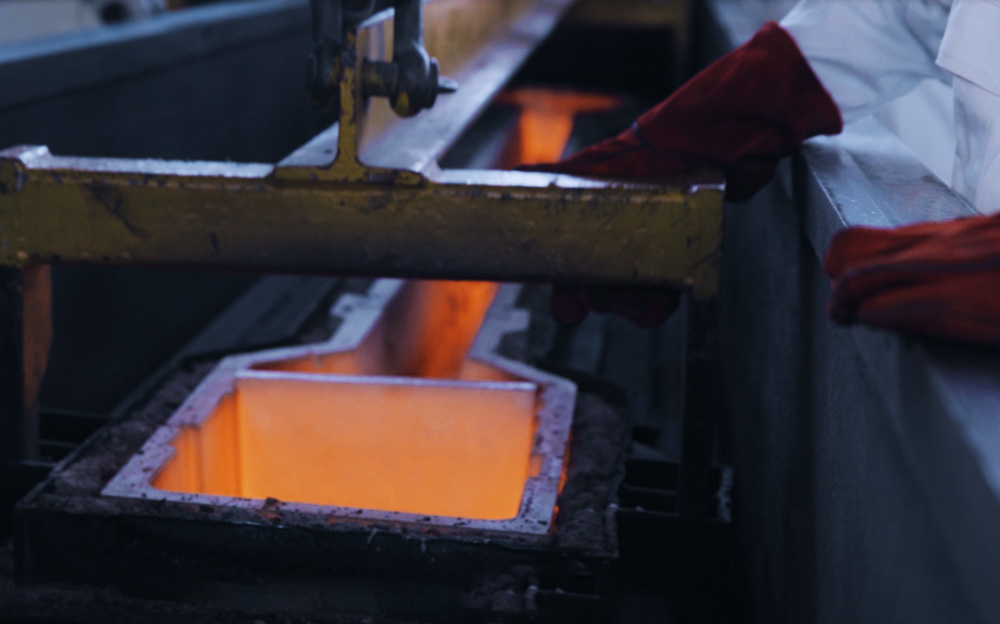
Ultra-pure superalloy melting technology
With the continuous upgrading of equipment technologies such as aero engines and gas turbines, their requirements for the performance stability and life of high-temperature alloy materials are increasing. Improving the purity of the material is the key factor to improve the homogeneity of the high-temperature alloy structure, to improve the consistency of the mechanical properties of the material and to guarantee the stability of batch manufacturing. At the same time, the ultra-pure high-temperature alloy has better casting performance. When producing high-quality large-scale thin-walled castings, it helps reducing the shrinkage related defects of the castings and filling the thin-walled sections.
ToLand Alloy masters the ultra-pure high-temperature alloy smelting technology including raw material pretreatment, high-purity calcium crucible making and smelting, de-sulfurization, deoxidization, etc., and realizes the integration of ultra-pure high-temperature alloy smelting technology. Using this technology, the company produced high-temperature alloys with sulfur and oxygen contents of less than 10 ppm, which is among the best in same kind of domestic manufacturers.
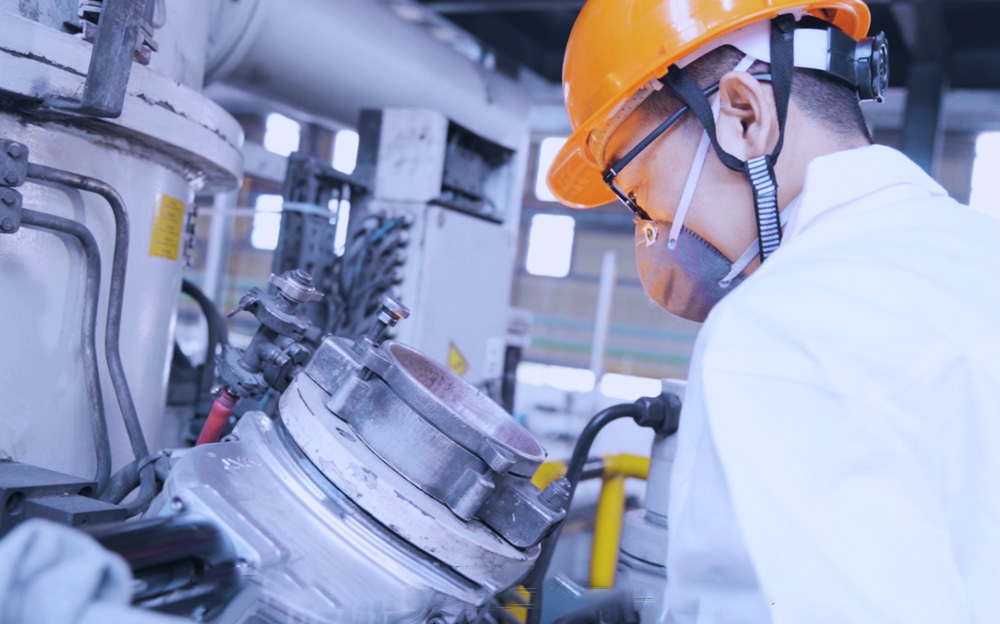
Structure uniformity control technology
With the development of high-end manufacturing, domestic deformed superalloys have entered into a stage of high-speed development, and the requirements for alloy structure and performance stability are becoming higher and higher. Homogenization and structure uniformity control technologies have become one of the development directions of deformed superalloys. ToLand Alloy adopts advanced remelting technology, high temperature diffusion annealing technology, combined with gradient variable temperature forging technology, forming a series of homogenized, structurally uniformed deformation high temperature alloy manufacturing technology.
Using the above technology, ToLand Alloy has realized the stable manufacturing and production of homogenized and evenly structured Nimonic80A rods. It has been used in high-performance marine diesel engine valves and successfully entered the international market to achieve batch production; ToLand Alloy has fulfilled the production of alloy homogenized and uniformly structured Inconel 690 and Inconel 600 rods. ToLand Alloy takes the lead in domestically manufacturing of high-quality heat transfer tube billets to improve the uniformity of heat transfer tube structure as well as mechanical properties. Such technology provides a reliable material basis for the stability of mass-produced products and improves the yield of finished products.
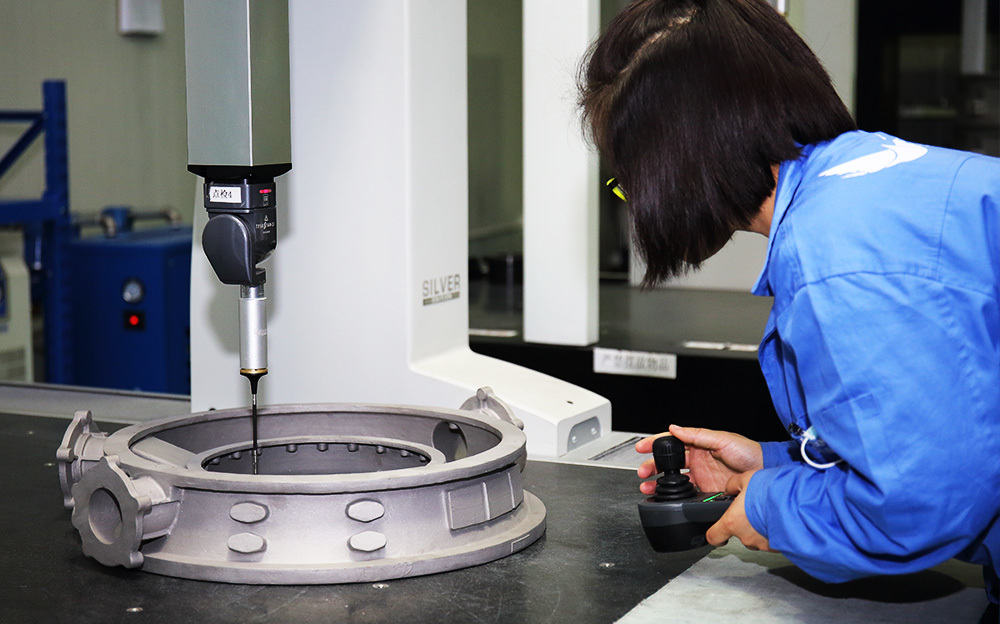
Near-net shape investment casting technology
The large castings produced by the traditional process have technical bottlenecks such as large machining allowance, thick walls, and overweight. It is difficult to meet the requirements of a large thrust-to-weight ratio in aero engines. This has put stringent requirements on the weight reduction of large superalloy structural parts. ToLand Alloy posseses international advanced technology and has established a comprehensive near-net investment casting precision casting technology system, covering computer-aided design and simulation technology, sectioning injection molding and integrated wax assembly, unique and efficient design of gates and risers,, ceramic shell making, and forming of complex inner casting structures , etc.
The above technology makes it possible to gravitational cast large and complex thin-walled structural parts, and overcomes the disadvantages of uneven material structure and unstable performance caused by centrifugal casting technology. Through the successful application of the precision investment casting technology for large and complex thin-wall castings, ToLand Alloy takes the lead in China to achieve mass production of large-scale high-temperature alloy castings with diameters greater than 1,000 mm and wall thicknesses less than 2 mm.
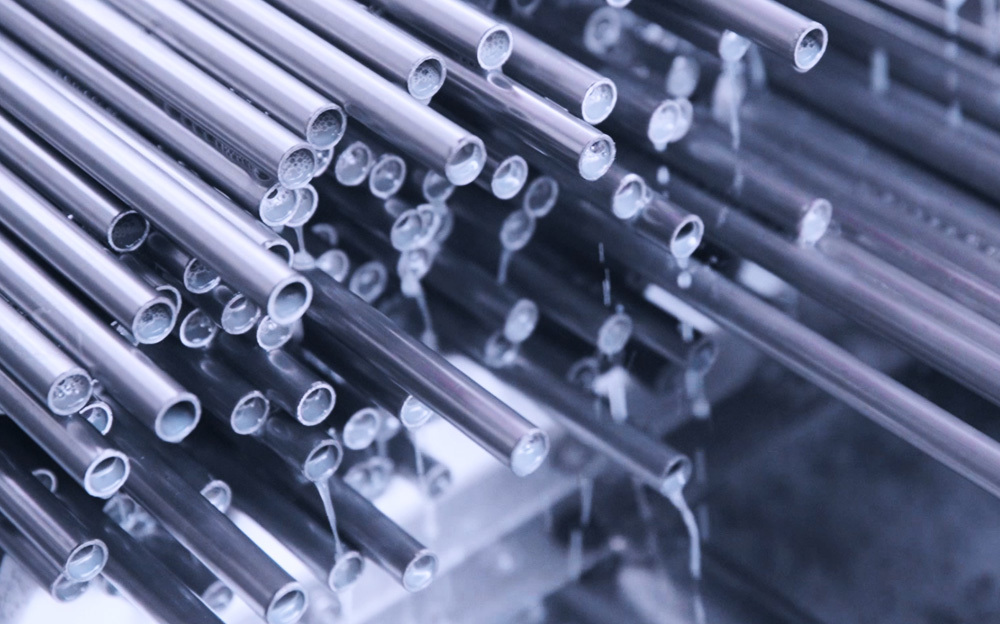
High-precision seamless tube manufacturing technology
Abandoning the shortcomings of the traditional tube manufacturing process and referring to the performance requirements of aviation industry tubes, ToLand Alloy has carried out independent high-precision seamless tube manufacturing technology development and technological innovation, forming ultra-pure tube billet smelting, high-efficiency hot forming, near zero Defect cold working deformation, vacuum and high-purity hydrogen atmosphere oxidization free heat treatment, safe and environmentally friendly ultrasonic degreasing, high-quality and efficient surface polishing, automated rapid non-destructive flaw detection and other tube manufacturing process technology integration. The company can manufacture high-quality high-temperature alloy and stainless steel seamless tubes with stable comprehensive performance, high dimensional accuracy and excellent surface quality.
The dimensional accuracy of the outer diameter and wall thickness of the manufactured seamless tubes can be controlled within ±0.03mm, and the inner and outer surface roughness (Ra) is less than or equal to 0.4μm. Our products has greatly improved service performance, and product quality has been well recognized by customers, ToLand Alloy has achieved a great reputation in domestic aviation tube market.
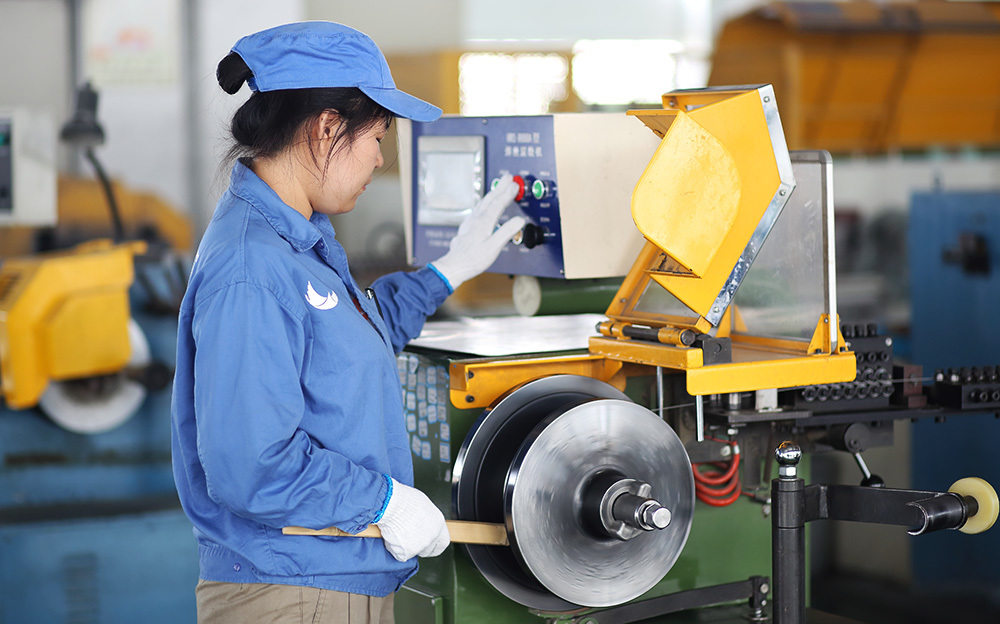
Multi-variety, multi-size fine wire manufacturing technology
Company independently integrates special smelting, forging and rolling, wire billets processing, wire drawing, bright processing, ultrasonic cleaning and other process technologies, to form an advanced full-process fine wire production line, which can independently produce wire products ranging Φ0.2-15mm with material of high temperature alloy, precision alloys, weld wire materials and so on. Company is capable of producing nearly 100 types of special wire materials research and manufacturing. The special weld wire produced by ToLand Alloy is widely used in high-end manufacturing fields such as ships, and special pressure vessels, and the product quality has been highly recognized by the industry.